Capt'n Wil's Diesel Polishing System
By Wil Andrews
Webmaster's Note: This article was originally
written for Trawler World Online, now known as Trawlers
& Trawlering. It is reprinted with permission
at the suggestion of Al Casanova who used the information
contained in this article to design the fuel polishing
system aboard Almar Too, his Nordic Tug 32.
You are free to use the information in this report in
any non-commercial way. The user is responsible to verify
that the information is suitable to his application and
takes sole responsibility for any use made of the material.
1 Gulf Coast Filter F-1
2 Gulf Coast Filter F-1 element
3 Gulf Coast Filter O-1 JR
4 Racor 500 2-micron element cut away to show filter
depth
5 Walbro 6802 continuous-duty diesel fuel pump.
The most common reason for marine diesel engines in general,
and recreational trawler diesel engines in particular,
to fail to run is associated with "bad diesel fuel."
The things that make the diesel fuel bad generally have
nothing to do with the original quality of the fuel. The
problems come about because of the condition of the fuel
we buy and what happens to the fuel when it gets stored,
sometimes at the suppliers' facilities, but most often
in our own vessels.
To get anything from this epistle, you must accept the
fact that this whole thing is a work in progress. The
work is to find out how to keep the fuel we burn Just
Like New. The progress in this work comes in fits and
starts, and next year I'm sure I'll know more about the
solution to the problem than I know now. Getting the whole
answer is difficult because while it is of vital concern
to us recreational trawler captains, it is a minor problem
when considered in light of the events of the nation and
world. There is no money dedicated to finding the solution
to this problem by either government or industry. There
are companies selling products proclaiming that their
product will solve the problem, but I am not aware of
any formal scientific studies that speak to the causes
and solution of this problem. That leaves it to amateurs
like CaptnWil, and others, to see this work in progress
to a conclusion for the recreational boating world. I
encourage all of you to make tests and keep records so
the whole body of information can be shared by all of
us. We make judgments based on our observations, experiences,
and faith in advice given by others. It is important that
we strive to be able to change those judgments when the
evidence suggests a change is called for.
I feel confident that many individual organizations that
have experienced this problem have come to a successful
solution for their particular situation, but they have
no reason to share their experience with us. That leaves
us pretty much on our own.
What follows is my final solution to my problem. I hope
it may be of help to you
Like most who have experienced bad fuel problems, I first
became aware that such a problem was possible in 1989
when my "new to-me," four year old trawler engine
quit while I was taking her home from a thousand miles
away.
The boat had spent two winters in Chesapeake Bay mostly
at the dock, made the trip down the ICW to the Keys, and
I took possession in Miami. The engine had less than one
thousand hours on it and the fuel tanks were less than
half full. With the joy that is only possible that first
day you own a boat, we set out with eight guests toward
North Carolina. Guests came and went along the way, and
thankfully, there were no guests when the engine stopped
underway the first time. Before I finally figured out
that the problem was a clogged fuel filter, and then found
the proper element, the engine stopped eight times. The
last time it stopped underway was in a passage that warns
not to anchor because of unexploded ordnance. For a lot
of reasons, that whole voyage is an experience I'll never
forget, but that's another story.
I did not know that this work in progress had really begun
until the engine stopped while underway again in Chesapeake
Bay that summer. It was an uncomfortable feeling to be
unable to move in the middle of the bay with night rising
on and the wind coming. By this time, I understood that
the symptom of the problem was a clogged fuel filter.
I recognized that the problem was most likely to occur
when the boat was in a seaway and the fuel got stirred
up. That realization brought terror to my mind when we
got caught in a July storm just off Cape Lookout with
60-knot winds and mountainous waves. If the engine had
stopped then, those I love the most would be cast into
the breakers of Cape Lookout.
Keeping the engine running is always preventing an inconvenience,
but sometimes it is a matter of survival. I continue this
work because of both reasons, but most importantly because
of the latter.
Early Efforts
After going through a Racor element every day for several
days, I decided to get to the bottom of the problem and
clean the tanks. The bottom of each tank had enough black
sand-like stuff to fill two five-gallon buckets each.
What was that stuff? It was the stuff at the bottom of
the tank. I have never had a satisfactory answer about
what it was. I am sure there were ways to find out, but
I have only seen speculation and theory about that stuff.
That speculation and theory led to putting an additive
in the fuel to prevent it from forming again which additive
is unimportant.
It is very popular today to think that something you can
pour into a fuel tank will take care of your fuel problems.
There is a large body of experience, including my own,
to indicate that any pour-in solution only treats some
of the symptoms, but that's not the real problem with
this procedure The problem is that while the immediate
symptoms may vanish, this cure begins to create its own
set of problems. If you kill the bugs, their dead bodies
will cause problems sometime in the future they just become
part of the jelly that wants to collect at the bottom
of the tank, and we know where that leads. If you emulsify
the water in the tank, it still goes through your injection
pump and injectors, and will lead to a whole new set of
problems.
We'll talk in a little while about the Polishing System
Solution, but if your system qualifies, you can get along
just fine without any extra system.
The Maintenance Supervisor of the North Carolina Ferry
System has been most kind and helpful to me in my investigation
of oil bypass filters and diesel fuel storage problems.
His observations and experiences are from many engines
on many automobile ferryboats that run long and hard.
They put more hours on most engines in a week than most
recreational boaters do in a season. They burn more fuel
in a month than we burn in a lifetime. When he tells me
his conclusions of his observations, I listen and believe.
The older ferryboats have Detroit engines and the newer
boats have Caterpillar engines. There are some facts about
the operation that have special meaning for us in seeing
why this operation doesn't have a fuel problem, but we
do:
1. The Ferry System buys diesel fuel
on State Contract and it is delivered directly from
the pipeline to his storage tanks.
2. There is never a time when the entire fuel supply
remains in the tanks more than a very few weeks. In
the summer, the cycle is not more than one week.
3. The engines on the ferryboats circulate a much larger
quantity of diesel fuel than they burn. They circulate
so much that all the Detroit engines and many of the
Caterpillar engines are equipped with coolers in the
return line to the tank to keep from overheating the
fuel in the tank. Keep this in your mind. It will come
up in a different light a little later.
4. The fuel in a ferryboat does not stay in the ferryboat
fuel tank more than a day when it operates and never
more than a few days in most other cases.
5. The engines are fitted with Racor diesel filters
with water separators and the normal fuel filters that
are supplied by the engine manufacturer just like most
recreational trawlers. Water separators are tended everyday.
6. At one time, a pour-in additive was used in the fuel.
During that time, high injector maintenance was experienced.
After a time, use of the pour-in additive was discontinued,
and after that cycle of injector maintenance was complete,
the injector problems decreased materially.
7. Fuel storage tanks on land are entered and cleaned
regularly.The most important thing to understand is
that the very high volume of fuel used and long hours
of operation in this installation, magnify everything
about the operation.
If you can guarantee you get clean fuel and guarantee
it will be stored in clean tanks and guarantee it will
remain in those tanks no longer than a week or two, you
won't need a Polishing System you already have the Absolute
Solution.
The amount of diesel fuel circulated by the system is
a very important factor in connection with our storage
problems. When I first started researching this fuel storage
problem, I heard stories that the Lehman-Ford 135 circulated
60 gph well, at least 30 gph. Wrong! No one knew the real
answer because manufacturers do not commonly provide that
information, and no one I ever talked to had ever measured
it. I was shocked to observe that the Lehman-Ford 135
returns 1.8 gph to the fuel tank at 2200 RPM.
I expect the high circulation rate story came from the
fact that Detroit two-cycle engines use circulated diesel
fuel to cool the injectors. Most four-cycle diesels in
the range of sizes used in recreational trawlers don't
cool the injectors with circulated diesel fuel so they
only need to circulate enough fuel to make sure the injection
pump always has a positive head. That is, the lift pump
must just pump enough fuel to guarantee that fuel is always
available to the injection pump at positive pressure.
This low flow rate has a direct bearing on our general
problem, but it also has a specific effect of the action
of Racor filter units that have what is called turbine
action. In most installations, the flow rate through the
filter is far too low to allow the desired turbine action.
It is possible that your engine has a greater pumping
rate than indicated above. It is a very simple matter
to measure the quantity of fuel returned to the tank.
Just break into the return line to the tank and catch
a known quantity of fuel in a known time and compute the
flow rate. You can do this at the dock with the engine
in neutral. Place a bucket under the return line and have
a large zip-lock ready to catch the measured fuel. Have
the engine started and increased the RPM to cruising speed.
Then catch fuel in the zip-lock for a timed interval.
The longer the timing interval the more accurate the results
will be.
Long-time CaptnWil readers will remember that one manufacturer
of these units threatened CaptnWil with legal action because
of dissatisfaction at not being able to manipulate the
way a West Marine Trawler Fest seminar was conducted.
For that reason, I will offer no opinions about these
devices. I will just say that a very effective Diesel
Polishing System can be fashioned without using these
units and the rest of this report will not mention them
again.
They are only mentioned here to let long-time readers
know the reason why.
It is generally agreed that water in the fuel tank causes
all sorts of hell. The experts tell us that algae is born,
lives, multiplies, and dies in the surface between the
water and diesel fuel. These critters and their residue
are a major source of trouble. The moral is: no water,
no algae.
Most of the water gets into our tanks by water condensing
on the inside surface of the fuel tank and less often
on the surface of the diesel fuel itself. This occurs
every time the temperature of a surface is below the dew
point temperature of the air to which it is exposed.
Without getting too technical, more moist air will have
a higher dew point temperature than less moist air and
be more likely to cause condensation. It is also helpful
to note that the condensation always occurs on the warm
side of the surface -- the beer glass sweats on the outside,
and your port lights sweat on the inside in the winter.
Thank God for the first, but lament the latter.
This all means that condensation can only occur in your
diesel tank when the temperature of the surfaces of the
tank and/or the diesel fuel itself is below the dew point
of the air INSIDE THE TANK. If you see condensation on
the outside of your tank or on your fuel lines, there
is no condensation going on inside your tank. The problem
can only occur when you don't see such condensation. Condensation
on the surface of the diesel fuel itself is seldom considered,
but is a fact. It works similar to fog at sea.
There are two ways to prevent condensation on a surface.
(1) Raise the temperature of the surface above the dew
point of the air or (2) Reduce the dew point of the air
below the temperature of the surface. Your automobile
defroster works like the first case and your air conditioner
works like the second case. Desiccant filters can also
be made to work like the second case.
The most common means to prevent condensation in fuel
tanks is to keep the tanks full. If they are full, there
is no air in them so no condensation can occur. It is
especially important to keep the tanks full when the boat
is idle for a period of time.
Desiccant filters in the vent lines have tremendous possibilities.
If they can be fitted properly, they will keep most of
the moisture in the air from entering the fuel tank, which
will lower the dew point of the air to very low levels.
Their installation and care in common recreational trawlers
offer some problems that I have not been able to solve.
The limiting factors include their physical size and the
requirement that they do not get contaminated with diesel
fuel. I hope someone will come up with a means of using
them with our diesel tanks because they could almost eliminate
the condensation problem in diesel fuel tanks.
There is more junk in fresh diesel fuel pumped from a
high volume supplier than I would ever imagine. That is
one of the reasons that engine manufacturers always put
diesel fuel filters on their engines. We seldom see this
crud because most modern fuel filters are spin-on types
with the element hidden from view.
I have a Gulf Coast fuel filter mounted on my pickup truck.
One of its features is that the top of the filter container
can be removed at any time for inspection of the element.
On a recent 10,000-mile land trip, I replaced the element
before leaving and had to replace it at 5,000 miles because
the crud in the element caused fuel flow problems on steep
grades at full load. During that trip, all fuel was purchased
at high volume truck stops.
It is one thing to get such dirt into a 20-gallon fuel
tank and quite another to get it into a 300 or 400-gallon
fuel tank on a trawler. The complete fuel turnover rate
in the 20-gallon tank guarantees that the entire contents
of the tank will be kept stirred up and the crud will
quickly end up in our fuel filter. In the 400-gallon,
on the other hand, the dirt will just settle to the bottom
of the tank like the silt in the delta of a river. It
will build there over time so that it can cause its worst
evil at our most critical moment.
Then there's that black stuff that begins by discoloring
the fuel filter, then discolors the fuel, then makes the
fuel black and puts jelly-like stuff on the fuel filter,
and then just shuts down the whole fuel system.
I can't find anything about this condition in the literature,
but I suspect it is the result of the solids from the
original crude oil settling out and returning to their
natural state. No matter what the cause, it is an ever-present,
ever-continuing condition that adds to that awful mix
at the bottom of our tanks. Let diesel fuel stand long
enough and it will turn black.
Except in rare cases, the factors that make our fuel storage
problems proceed at a very slow pace. It may take months
or years for the problem to become evident, but when it
shows its ugly head, it is "full growed up."
It is mean and ugly and spoiling for a fight. Remember
that the first time it happened to me there were ten-gallons
of crud at the bottom of each fuel tank.
The important thing to remember about my first experience
with this problem is that just removing the symptoms did
not remove the problem. The problem came back three years
later.The second time it happened to me I vowed to solve
the problem so I would not get the symptoms.
While it now seems obvious, the real objective escaped
me for some time in this venture. The objective is to
return and/or keep the fuel just like new. That's just
what the NC Ferry System does by their high turnover rate.
But that statement needs to be refined a little. We need
to determine just where we want to make the fuel just
like new. The answer to that question will determine where
our design goes.
The common system with one secondary and one primary fuel
filter tries to keep the fuel that enters the injection
pump just like new and the only effect on the remaining
fuel is the returned clean fuel. Once we understand that
most of our engines return very little fuel to the tank
it becomes obvious that this system has little or no effect
on the fuel in our tank. The fuel in the tank keeps getting
less and less just like new, and filter replacement intervals
decrease.
Depth type filters provide better filtration than edge
type filters and are available with much larger capacities
than edge type filters. Like most on this list, I was
introduced to depth type filters very late in the game.
I did not even know of their existence until after I initially
solved my fuel problem with a polishing system using a
Racor edge type filter.
Gulf Coast Filters (GCF) manufactures the depth type filters
I have experience with, but there are many other manufacturers
of such filters. I have every reason to expect that those
filters perform well.
The basic concept of the depth type filter is that the
fuel passes through a lot of filter media. For example,
the fuel travels from one end of a roll of paper towels
to the other as it passes through a GCF F-1 fuel filter
thus the depth. It is that eleven plus-inches of contact
with the filter media that makes this filter so efficient.
It is its huge volume, when compared to the volume of
a Racor-500 or 900 that gives it such an impressive capacity.
Depth type filters are not required for the diesel polishing
system, but they will increase the efficiency of the system
and reduce the maintenance. I will describe the application
of these filters as we go along, but you can just substitute
any other quality filter you desire.
I do not have a separate polishing system and a normal
fuel supply system. I modified the existing fuel system
to incorporate the polishing capacity into it.
I also recommend that a single fuel/polishing system supply
all the fuel to every engine on the boat. If your total
diesel circulation requirements are not more than 60 GPH,
a single Racor-500 or GCF F-1 will handle your needs quite
well. Systems that require greater circulation rates are
beyond the scope of this report and will not be covered
here. CaptnWil will be happy to discuss designs for such
systems if desired.
The system consists of the appropriate filters connected
to a continuous duty electric fuel pump with the piping
arranged to circulate the fuel from the tank through the
filters and back to the tank.
The system has evolved over the almost two-years that
I have been investigating this problem. That evolution
has come about as I have learned more about the subject
from my own observations and the experiences of others.
The single most important discovery is that a great amount
of circulation is necessary to keep a substantial quantity
of fuel just like new. My pump circulated about 50 gph
and it ran at least 48 hours every week. With a fuel capacity
of 600 gallons, I turned the fuel over a little more than
three times per week. Continuous circulation is not too
much.
The major components of the system are:
1. Walbro fuel pump.
The factory phone number is (517) 872-2131. I bought
mine from Peterson Co whose phone number is (800) 537-6212.
This little pump is protected by a five-amp circuit
breaker so it draws hardly any current. It is marketed
to replace the original diaphragm operated fuel pump
on diesel engines and is rated for continuous duty.
If you choose another pump, make sure it is rated for
continuous duty.
2. Gulf Coast Filters F-1 fuel filter and water
separator. The phone number is (800) 398-8114.
This filter is recommended to be the main fuel filter
if it can be fitted in the space. It uses a roll of
Bounty paper towels. The element replacement cost of
this filter is always attractive, but if you have a
very dirty system to clean up, you will appreciate it
even more. In addition, it filters in the sub-micron
range and will add life to your injection pump and injectors.
This filter has the best water separator I have seen.
It is efficient and very large.
The only drawback about this filter is the vertical
clearance it requires. It must be mounted vertically
for the water separator to work. The whole thing with
clearance above the filter requires about 33 inches
of total vertical clear space. The vertical clearance
can be reduced to about 24 inches if a tilting mount
is fashioned to facilitate removing the element.
If you can make it work, your troubles will be rewarded
with a marvelous filter.
This filter is rated at 250 HP and can be paralleled
if the engine capacity is above that.
3. Gulf Coast Filter O-1 Jr. If you
can't make the F-1 fit, you can use a Jr. It was originally
designed as a small bypass oil filter, but can serve
very well as a fuel filter.
It comes with a molded-in orifice to restrict the flow
in oil bypass work. If you use the filter for fuel,
drill out the orifice. I use one on a 180 HP engine.
This unit uses a roll of toilet paper as the element
and can be fitted most anywhere in any position. Its
drawbacks are that it has less capacity than the F-1
and does not have a water separator. If you use this
filter, you must make sure a water separator is in the
system.
4. Racor Filter and Water Separator.
If you choose not to use either of the GCF units above,
you will need one like the Racor. This unit is well
known to all and is available from many sources. The
larger the size the longer the element will last, but
its capacity will be very small, and its element replacement
cost will be large when compared with the GCF filters
above.
The Racor water separator works fine and the element
won't pass water. Be sure to use the 2-micron element
in this and any other work.
There are other similar units on the market and I expect
they work fine, but I don't have experience with them.
Of course, Racor elements can be obtained almost anywhere
there is water.
5. Tubing, Valves, and Fittings. Type
L soft copper tubing or USCG-approved hose can be used.
The copper is better, but the hose is easier. I went
with the hose. I suggest flare fittings for either material.
Use the same size lines as is on your fuel system now.
Several valves are in the system. The West Marine catalog
lists _-inch ball fuel valves that I like and also conventional
Tempo fuel valves. Either will work well. Use Loctite
242 on the screw fittings. I've never had a leak with
this stuff.
Two vacuum gauges are specified. Every vacuum gauge
must be fitted with a shut-off valve. If the gauge doesn't
have a shut-off valve, and it breaks, you can't run
the engine and if you have a bottom outlet fuel tank,
you run the risk of emptying the fuel tank into the
bilge. Do Not! I say, Do Not use the Racor gauge that
replaces the T-handle. It cannot be fitted with a shutoff
valve.
A check valve will be included in the piping diagrams.
It can be obtained from most local shops that do diesel
injector pump and similar work. Its use will be discussed
in the circuit description section.
6. Timer. While a timer is not required,
providing one costs little. I used an Intermatic Spring
Wound 12-hour Timer Switch, model FF12HH. It provides
a disconnect switch as well as a 12-hour timer. I bought
mine from Grainger.
A basic fundamental in designing a diesel fuel system
for any boat is to design the system so that the boat
will not have to stop if a fuel filter gets clogged or
an instrument breaks. There are many situations where
not having engine power is extremely dangerous. It is
so dangerous that the Rules Of The Road have a special
category and rules for it, "Vessel Not Under Command."
It is necessary to design the piping so that just adjusting
a few valves will allow fuel to flow so the vessel can
remain under command.
This basic requirement is at the heart of the diagrams
shown. It is the reason that valves are shown for each
vacuum gauge and the reason for the two-filter arrangement
in both diagrams.
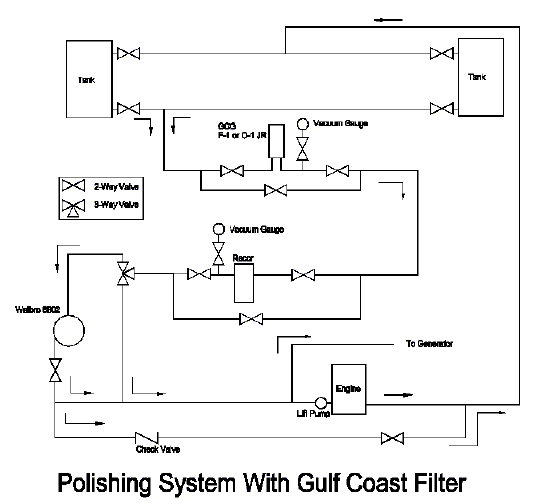
You will notice that the
GCF F-1 and O-1 JR. are piped in series with a Racor in
"Polishing System With Gulf Coast Filter." This
is possible because the F-1 and JR will filter particles
much smaller than the Racor and the Racor will remain
clean almost forever. If the F-1 gets clogged up, you
may safely bypass it with its bypass valves and just use
the Racor until you are in a place to replace the GCF
element. In like manner, if the Racor gets clogged up
you can just bypass it and operate on the GCF alone until
the Racor element is changed
In "Polishing System With Racor Filters," the
Racor filters are piped in parallel because they have
the same filtering efficiency.
In both cases, the vessel
can continue underway by adjusting the valves.
Everything possible should be done to keep from having
to make filter changes underway. That is the purpose of
the vacuum gauges. If they are inspected often they will,
in most cases, give ample warning so panic actions underway
are not necessary. The bypass piping allows for the unexpected
situation when it occurs.
It is recommended that the Walbro fuel pump be operated
all the time the engine is operated in addition to any
weekly pumping schedule as required. This will mean that
you are polishing the fuel any time you are underway.
If you are on a cruise that means you may not need to
operate the polishing system on its weekly schedule. You
can just operate on the weekly schedule when the boat
is idle.
In any event, you should pump enough to turn the fuel
over at least three times per week. More is better than
less.
I try to avoid using check valves in any piping system
where possible because they are prone to fail because
of crud accumulating on the working parts. This system
uses a check valve that lives in the very clean diesel
fuel that we have just polished. It should stay clean
and have a very long life.
The system is designed so that the Walbro just keeps a
positive head on the engine lift pump while underway and
bypass most of the fuel around the engine. If the Walbro
were to fail while underway, the engine lift pump would
try to draw fuel from the engine return line and the engine
would stop running because of air in that line. The check
valve will prevent that problem. The two-way valve in
the same line can be used to close the return as well,
but the check valve just makes it more convenient.
The three-way valve is provided for those who do not want
to run the Walbro underway. In that situation, turn the
three-way valve to the proper position and adjust the
two-way valve in the line that has the check valve.
This is a CaptnWil Law when using the polishing system:
Return the fuel to the same tank it came from.Any other
procedure may lead to a fuel spill. That means making
sure the valves at the fuel tanks are always set properly.
Other pumping arrangements may be more efficient at cleaning
up the fuel, but the risk of a fuel spill removes them
from consideration.
Day tanks have become a popular topic of late, and a few
words are necessary about them in connection with a fuel
polishing system.
The object of a day tank is to provide a "day's"
quantity of fuel that is guaranteed to be clean and dry
for the engine. Sometimes it is used to overcome the problem
of excessive suction heads on the engine lift pump.
It is important to remember that the clean and dry fuel
in the day tank will be exposed to the same conditions
that cause the fuel in the main storage tank to become
bad. Given enough time, the fuel in the day tank will
get to the same condition as the fuel in the main tank.
A filter and a water separator are still required on the
outlet of the day tank.
To provide the desired results, this tank must, in fact,
be a "Day Tank." That is, the fuel in this tank
must remain there for only a short time. All the problems
of long-time fuel storage in the main tank will be present
in the day tank if fuel remains in it for long periods
of time. Once it ceases to be a "Day Tank" it
must be treated just like any other tank.
All of the usual safety wiring practices should be followed
and the pump should be protected with a 5-amp fuse or
circuit breaker. It will be convenient to locate the switch
or timer close to the helm.
Used Gulf Coast Filter
F-1 element and Racor 500 2-micron element:
F-1 element shown after 500 hours with clean fuel.
Racor element cutaway showing pleating of element.
Wil Andrews has a passion for testing equipment and developing
systems.
For years, Captn Wil, as he is widely known, has applied
his engineering background in the search of the best in
diesel polishing, anchors and other systems for trawlers.
Recently, family health considerations led to the sale
of AfterSail, a Krogen 42, but Captn Wil continues to
be an active and respected participant on Trawler World
List.
When you see the signature Captn Wil, you better be ready
to toss preconceived notions and advertising claims out
the porthole.
Much of the equipment testing and system development undertaken
by Wil Andrews was accomplished aboard his beloved AfterSail,
a Krogen 42 Pilothouse.
|